The value of a supply contingency plan
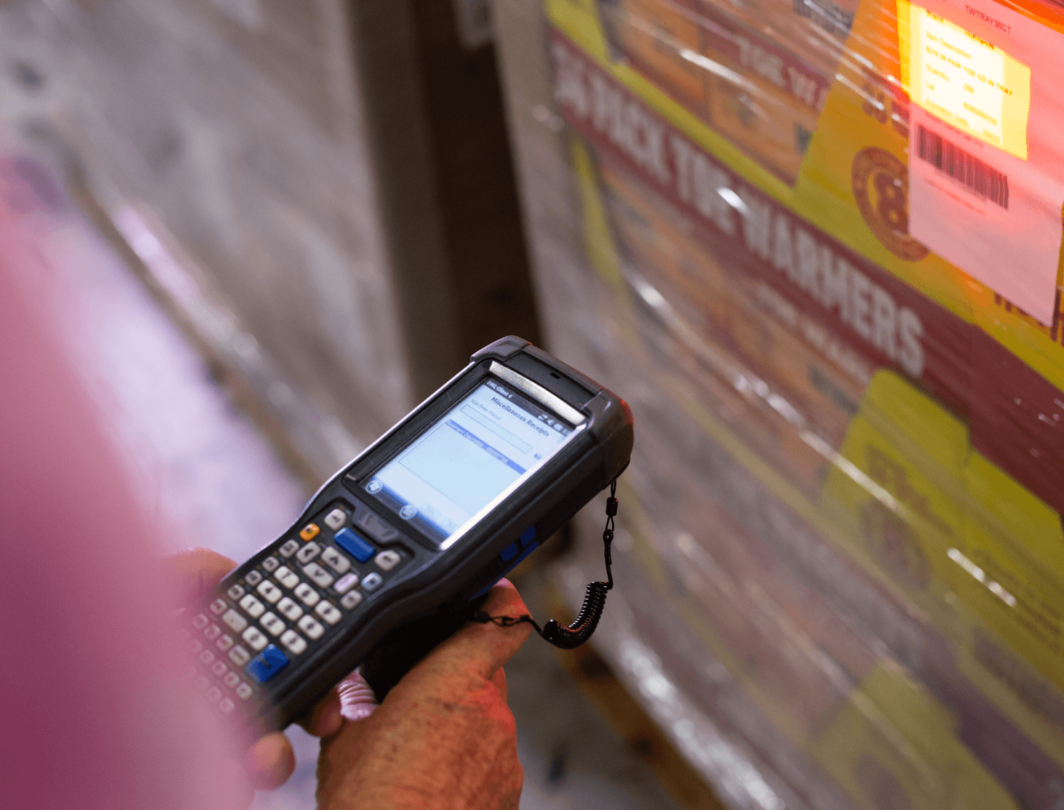
The coronavirus (COVID-19) outbreak is affecting people and businesses on a global scale. For the latter, there have been many effects, one of which is of how vulnerable to disruption our global supply chains are.
Exponential growth in trade over the past few decades means today’s global supply chains are incredibly complex, with manufacturers and distributors vulnerable to any sort of disruption. For example, China was the first country to suffer significant disruption as a result of coronavirus, meaning travel restrictions, labor shortages and logistical challenges have already impacted supply chains.
Pandemics are unique. Where you may well have risk management processes in place to deal with controllable and foreseeable challenges, such as compliance, financial and capacity issues, they could struggle to prepare you for world-defining events.
For example, you may need to cope with less staff, a dramatic decrease in productivity, and a change in how your customers decide to spend. And with China being such an essential and influential part of global supply chains, there are inevitable consequences.
How coronavirus is affecting supply chains
According to Gartner, you may have already seen or will see supply chain impacts such as:
A shortage of materials
You may suffer supply shortages of materials or finished goods coming from logistical hubs in impacted areas.
A shortage of labor
If you have a presence in an affected area, you may have problems with finding people to work because of quarantine guidelines or illness. In the UK, travel is becoming limited, with social distancing and quarantine requirements significantly affecting labor, which then leads to sourcing and logistical challenges.
Sourcing challenges
Finding new business or making new agreements will be challenging with restricted travel in affected areas.
Logistical challenges
Your established hubs and supply networks could experience issues when it comes to capacity and availability, so your materials could get stuck, especially if you have difficulties finding new routes and modes of transportation.
10 business continuity planning steps to take now
So, in terms of contingency planning, what should you do in the short and medium term, and what steps can you put in place to make sure you’re as prepared as possible in the long run? Here are 10 things to consider and do.
- Consider your people – their welfare is paramount, and they are a critical resource to your business. You may have to rethink work practices. Look at who can work from home and who needs to be present on the front line.
- Monitor what’s happening to your supply chain in countries affected by coronavirus. If you don’t have full visibility, prioritize getting this in place as soon as possible.
- Build an in-depth and detailed emergency operations structure and process at the plant level, with predetermined action plans for communication and coordination, designated roles for employees, communication and decision-making protocols, and emergency action plans that involve customers and supplier.
- Make sure inventory is in reach and outside impacted areas and logistical hubs.
- Work closely with your legal, finance and HR teams to understand what it’ll mean financially and legally if you can’t get supplies to customers.
- You may have to put in additional steps to contractual arrangements with customers. If you can’t meet your obligations, a clear understanding of your contractual terms will allow you to plan and prioritize your response.
- Look at ways to balance supply and demand while building a buffer when it comes to stock.
- You may need to find ways to diversify the suppliers you need and revisit the whole way you treat risk management.
- Work with stakeholders and your most critical suppliers to prepare for potential material and manufacturing capacity shortages.
- Review business forecasts and run scenarios to determine where you are at risk now (and may be in the future).
Adapt your long-term supply chain strategy
Once the initial impact of coronavirus has been alleviated, you should understand that it’s going to take some time for the full repercussions to present themselves.
Then it’s very much about preparing in case a similar situation occurred again. If you take actions such as scenario planning exercises, for instance, you can create action plans and put in steps to diversify your supply chain and source alternative supplies.
Coronavirus is a significant disruption, but today you may have to accept that disruptive events are the new normal. After all, the headlines were only until very recently full of human-made events that affected the supply chain such as trade wars and tariff wars.
If you’re looking to handle disruptive events better in the future, it’s not enough to think about supply chain strategy conventionally. You’ll need to rethink logistical strategy and manage supply chains in a way where you’re anticipating disruption rather than just merely responding.
Be clear on the processes of all your suppliers, even those upstream and several tiers back. If you don’t, your business is less likely to have the ability to respond or estimate impacts, as you are unfamiliar with upstream suppliers.
Understand where your critical vulnerabilities lie. Your supply chain may have a dependency that puts your business at risk if a wide-ranging issue occurs. Say, for example, you’re dependent on a supplier with a single facility and a large share of the market. If a significant problem happens (anything from your supplier going out of business to a pandemic occurring), you’ll be left with massive difficulties.
Rethinking the design of your supply chain
Many organizations build supply chains with globalization in mind – the assumption has been that global trade allows us to source, produce and distribute products from locations with the lowest cost. However, the likes of Brexit, the US/China tariff war and now coronavirus will make us think again, especially if suppliers are located in a central location far away.
Today, we may be looking at an era of new supply chain design where businesses can be ultra-agile and responsive in dealing with changing policies, regulations and natural disasters.
Redesigning your supply chain is a complex undertaking. But having a backup capacity for supply, production and distribution means you reduce the risk of your entire supply being disrupted. The second and primary sources should ideally be away from each other. This will decrease your risk but could lead to an increase in costs. Similarly, having production facilities with local sources of supply spreads the risk and could cut transportation costs.
It’s impossible to anticipate the arrival of global crises such as coronavirus, but businesses can mitigate their impact by improving their supply chain preparedness. By putting the right plans in place before a disruption occurs, and testing and learning before the fact, you’ll put your business in the best possible position to keep moving and hopefully weather the storm.
This article is part of our Managing uncertainty series which offers practical advice and support to help you keep your business moving as we all navigate these unprecedented times.
Ask the author a question or share your advice