The future is here with wearable devices and the smart factory

What will the workforce look like in the age of Industry 4.0 and the increasing digitisation of manufacturing? Can we already visualise what the shop floor of the connected smart factory will look like and how wearable devices will make an impact?
Future-gazing can be guesswork to a certain extent, but the facts and active movement by businesses point to digitisation, automation and data collection being beneficial to them, improving efficiency at the same time as keeping costs low, leading to better experiences for customers.
According to technology and services company Aberdeen Group, best-in-class companies (top 20% based on performance) are rapidly implementing Internet of Things (IoT) capabilities twice as fast as all other companies.

Source: IoT and Analytics: Better manufacturing decisions in the era of Industry 4.0
These IoT systems can collect manufacturing data in a transparent, comprehensive and interactive way. They provide real-time visibility into assets and equipment, quality of processes and factory resources.
It’s much easier to visualise the whole process digitally. Many people understand the idea of how data can produce digital factory simulations that predict how a product is expected to be manufactured. Less understood is the idea of a “virtual factory”, which is a real-time simulation of how production is actually being manufactured.
A virtual factory can provide a role appropriate, operational view of the entire factory floor (including plant, processes and equipment, etc) for anyone, anytime, from anywhere. This virtual factory can be the cockpit for piloting and improving a factory.
Interest in wearable devices
James Woodall, chief technology officer of software development house Intoware, understands the potential of the virtual factory and the transformative power of data and IoT in the enterprise space.
A firmware developer with experience of working with wearable devices for nearly 10 years, he initially worked on the Golden-i, a headset targeted at large industries such as manufacturing and healthcare.
“We spent a lot of time to make sure that wearable devices had a use – up until then, they were a bit form over function – technology which had been invented, but which few people knew what to do with”
James says: “There was little documentation when it came to developing wearable devices back then. This meant my team ended up doing a lot of wearable research and inventing a lot of new, different interface paradigms. I have about six wearable patents around software for wearable devices.
“I ended up talking to a lot of customers who were interested in wearable devices. User cases they talked about included workers having hands-free instructions and hands-free communication.
“For example, if you’re an industrial telecoms worker on a phone mast, the last thing you want to do is be holding a tablet or laptop. You want to be hands-free to do your job.
“We then spent a lot of time to make sure that wearable devices had a use – up until then, they were a bit form over function – technology which had been invented, but which few people knew what to do with.”
Sage Business Cloud X3
Need better insights into your business? Sage Business Cloud X3 provides you with fast, simple and flexible business management, helping you to manage your business and boost your profits.

Removing paper reports from the equation
The idea of using wearable devices for hands-free instructions and communication is a clear, practical application of the technology. Workers in the oil, gas and automotive industries, for example, often have complicated, documented instructions. With paper, it’s difficult to know whether instructions had been followed correctly as there is no audit trail.
The software product that Intoware has built – WorkfloPlus – allows employees using apps on different devices (wearables, smartphones, tablets, etc) to provide reliable enough information to show that a process has been followed correctly.
He says: “If a building is said to be inspected and I’m handing a piece of paper with a signature on, you don’t know whether it has truly been inspected, because all you have is a piece of paper.
“This could be a problem, because there’s a disconnect between what really happened and what a report says. There have been incidents in the past where train crashes have occurred due to tracks not being inspected. But there’s documentation exists which says they were.
“What we do is intellectually straightforward but quite complicated in practice. We make sure that when people are inspecting machinery, that any faults are indicated to the right person straight away.
“Previously somebody might have a clipboard and pen, with any errors found updated through a spreadsheet and the relevant person informed through email. With our software, the people who need to be notified are informed immediately as the inspection is being done.”
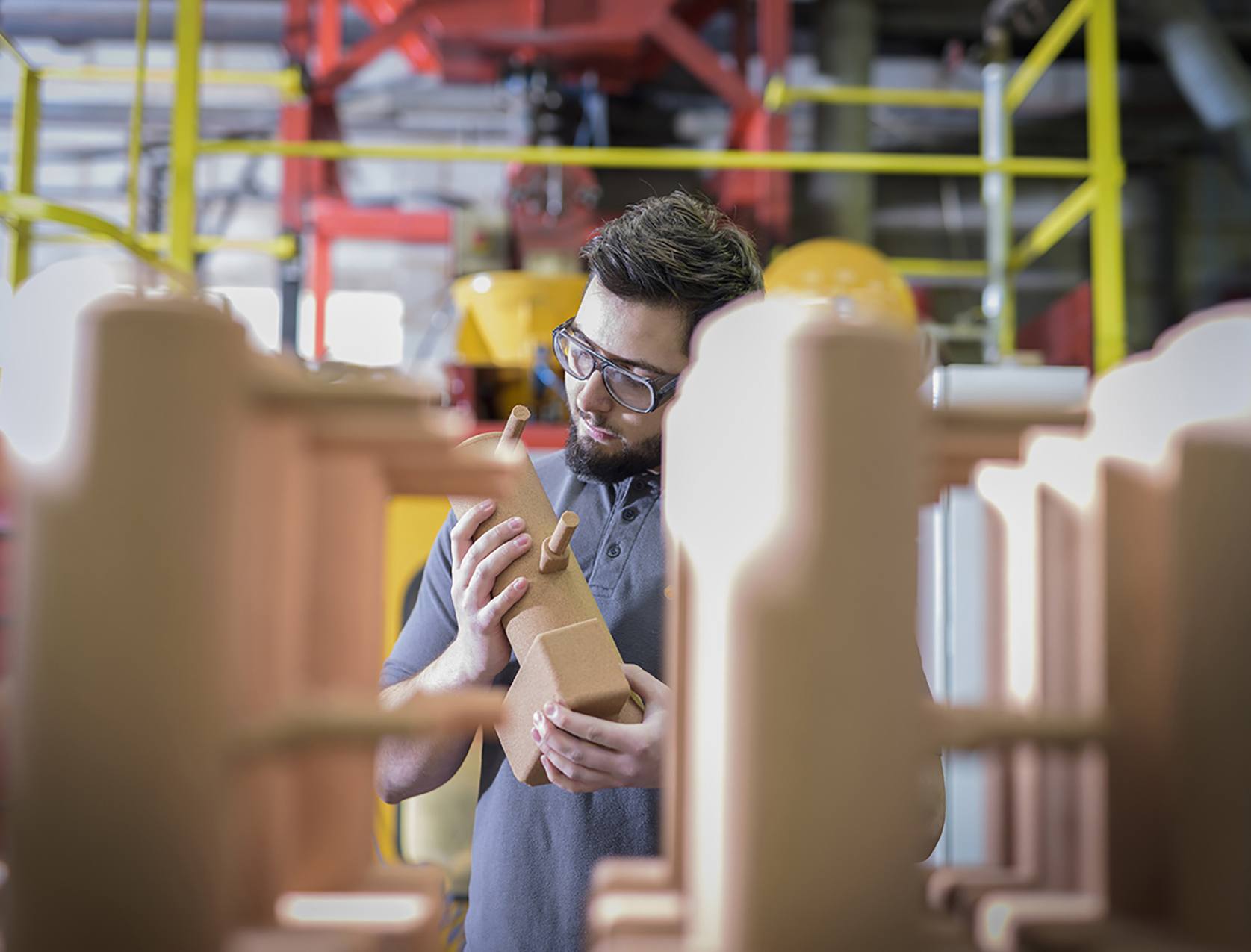
People are one the piece of the puzzle when it comes to having a productive business
Power of people, hardware, software and connectivity
An organisation’s use of WorkfloPlus is a good example of how businesses should look at four strategic pillars – people, hardware, software and connectivity – to make their companies productive when it comes to the use of technology.
To make digital transformation work, your business needs to think about how innovation will benefit your workers, find a marriage between hardware and software that works, and make sure everything is connected to make use of data.
WorkfloPlus is very Industry 4.0 in the sense that companies can use data to gain insights on a process – for example, you can see whether a process that should take one hour takes much longer and has gone wrong. Bots can be trained to identify where the anomalies might be, without requiring humans to look at the data.
“Inspection data needs to make its way into an ERP system. With a desktop computer and paper, there may be an inefficient gap between marking an inspection checklist with a clipboard and the typing of information”
James has spoken to many C-level executives in various industries and says the use of technology such as WorkfloPlus comes down to two factors: whether it can reduce cost through an increase in efficiency and if it can improve health and safety.
He says: “We have a very large automotive parts manufacturer as a client. They save time and increase efficiency as they know a parts inspection procedure is followed properly every time. These benefits are easy to calculate – we know that by using our technology, they’ll save a certain amount of time every day.
“The health and safety of workers is also important. During building work, builders often tape up smoke alarms because they are activated by dust, and left taped up once the work is done by mistake.
“Our software will help from a safety and compliance perspective, because our software forces a builder to go through a process where they un-tape the smoke alarm and leave it uncovered.”
Using wearable devices for inspections
James describes how software like Intoware could integrate with a modern ERP system: “In the food manufacturing industry for instance, inspections need to happen to make sure everything is compliant and health and safety rules are followed.
“That inspection data needs to make its way into an ERP system. With a desktop computer and paper, there may be an inefficient gap between marking an inspection checklist with a clipboard and the typing of information.
“The problem is that the data may be stale, or inaccurate. If there’s half an hour between doing the inspection and putting it into a system, a lot of things happen – maybe paper gets wet, smudged or lost for instance.”
“With our WorkfloPlus, they could perform the inspection with a wearable, tablet or smartphone. Enterprise management can make good use of this real-time for other business applications.”
The importance of the cloud
Software that works on mobile devices and works with data like WorkfloPlus shows the important of the cloud, which allows the physical and the virtual to communicate more closely than ever before. Closed systems are being replaced by open systems that allows collaboration between different disciplines for more productive outcomes.
The cloud underpins Industry 4.0, enabling data connectivity on a global scale, moving data from on-premise servers to cloud-based databases that allows your organisation to access their data from anywhere in the world. It frees your people up from needing support infrastructure, with a cost model based on usage.
Rather than simply preparing for cloud technologies, James says manufacturers should be actively investigating and innovating with them. Many vendors offer solutions that are still relatively immature, and it’s tempting to sit back and wait for markets to mature.
However, it’s the early adopters who will see the early benefits and gain a competitive edge.
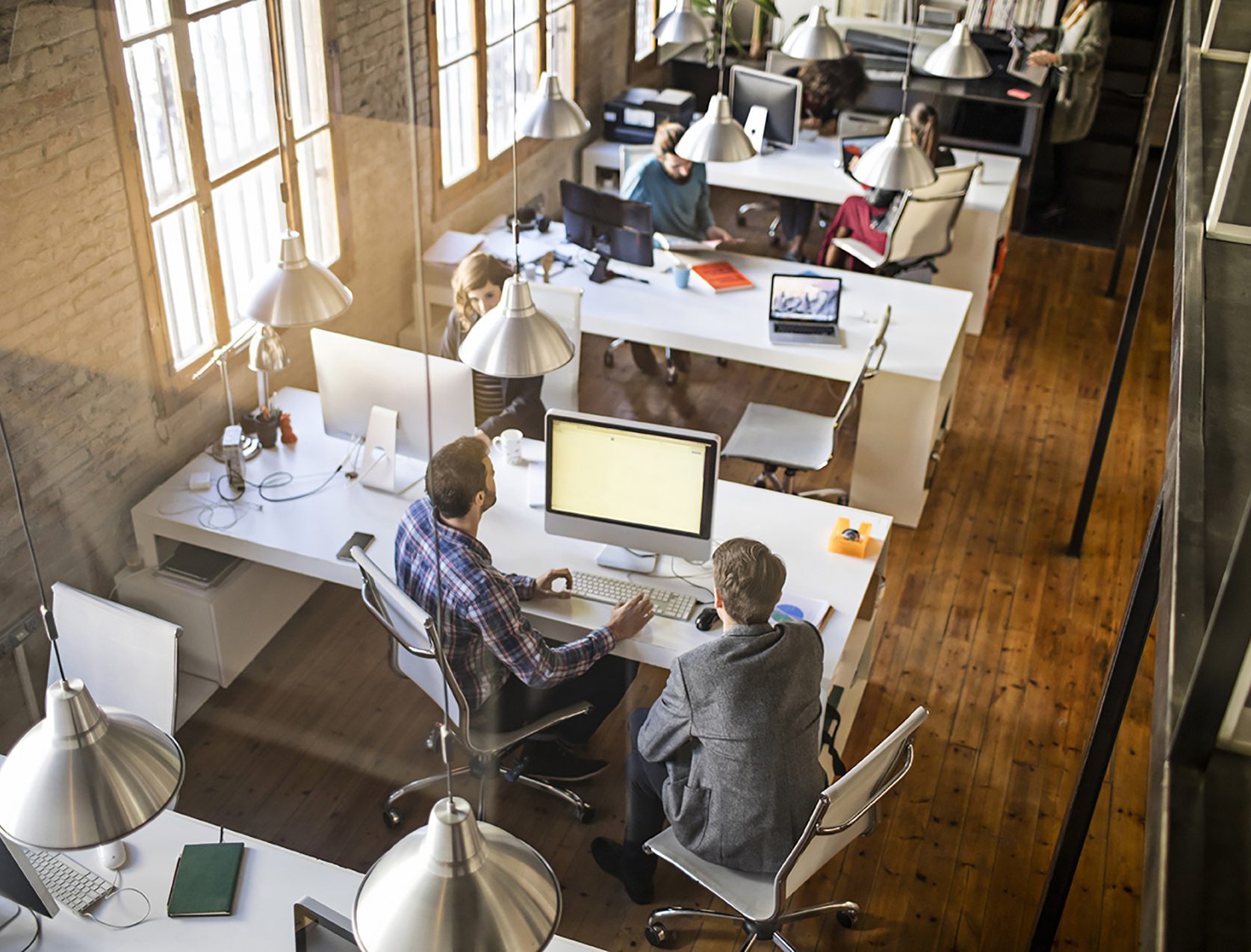
Consider big data and predictive analytics, AI and the smart factory to stay ahead of the competition
What CTOs need to do now
When it comes to Industry 4.0 and cloud innovation, James advises you to think about:
Big data and predictive analytics
By taking data from various sources, manufacturers can analyse it to great benefit – for example, predicting failures based on historical trends can make a huge difference when it comes to limiting unscheduled downtime.
Predictive analytics means manufacturers can move away from having a periodic, scheduled maintenance of machines, and towards auto-scheduled maintenance when something concerning is detected from IoT sensors. The more data analysed, the smarter the decisions.
Interoperability
This describes how every aspect of a factory – people, machinery, devices, sensors and hardware – are connected and communicate with each other.
Again, think about the virtual factory – a real-time virtual copy of the physical asset, system or infrastructure, created by collecting data from sensors across the physical entity. IoT sensors enable interoperability – by taking sensor data and moving it to the cloud, the processing of this data is much easier to achieve.
Technical assistance
Cyber-physical systems can conduct tasks that are unpleasant, unsafe or too physically challenging for humans to carry out, or collect, aggregate and display data in support of decision making and problem solving.
Decentralised decision-making, machine learning and AI
With the cloud and Industry 4.0, you can grant cyber-physical systems the ability and permission to make simple decisions. Machines that learn and make decisions (AI) can deliver both efficiency benefits and higher-quality products – resulting in higher revenue.
AI and, more specifically, machine learning can navigate datasets that are too large, too fast and too complex for machines to analyse and understand. It can draw insights into manufacturing processes that were previously too subtle to find – and with the cloud, you can analyse machines in multiple factories and countries.
Enabling machines with AI also allows them to learn and adapt to changing environments and demands without the need for human interaction, reducing downtime.
The smart factory
Building a connected factory floor should mean costs are reduced due to less material waste, lower personnel and smaller operating costs. The smart factory can be more agile, delivering high quality and fast production that is responsive to customer needs, bringing them more granular and up-to-date information.
James says: “Moving towards the smart factory doesn’t have to mean a complete overhaul with huge upfront investment. Sensors can be retrofitted to existing machinery, so choose from your existing infrastructure, investigate vendors offering IoT retro-fitted solutions and trial it.
“Of course, you’ll only get the full benefits of Industry 4.0 from committing to all its elements.
“Don’t pick a technology and work backwards to look for a problem to solve with it. Think about your biggest pain points and areas where a successful point of contact would really make a difference, and then see if AI, Industry 4.0, cloud or even other technologies such as blockchain could address problems.
“Also, look to see what other companies in your sector are doing with these technologies to help kick-start some ideas.”
Ask the author a question or share your advice